所在企业名称:伦茨(上海)传动系统有限公司
对于设备制造商来说,设备是商业模式的核心资产,也是和客户沟通的的关键点。所有增值流程(如工程、生产、销售、服务和维护)都以机器为核心,随着工业物联网技术的发展,直接获取设备关键数据,以改善和提高设备和生产线的性能,变得越来越重要,基于此目的,在一汽红旗汽车涂装四车间,采用伦茨的提供的软硬件服务,建立了一套变频器数据采集与监控系统,实时采集现场所有变频器的数据,比如电机的速度,电流和扭矩等,变频器的型号、固件版本和故障代码等信息,并将得到的数据进行存储,展示或者数据分析,以达到如下目的:
● 减少设备维护时间
● 资产管理
● 支持现场服务以及备件替换等工作
● 更好的了解生产线的状态
● 提升工艺性能及OEE
● 远程程序及固件下载
● 预测性维护,识别生产线的健康变化,及时发现异常
这是伦茨产品在汽车行业的一个典型应用,近千台分布式变频器以及柜装变频器应用在一汽红旗汽车涂装车间的输送线中,所有变频器通过Profinet总线连接到西门子PLC中,网络拓扑结构为星型或者线型,如何对现场变频器海量数据进行有效采集和存储,是这个项目成功的关键所在。
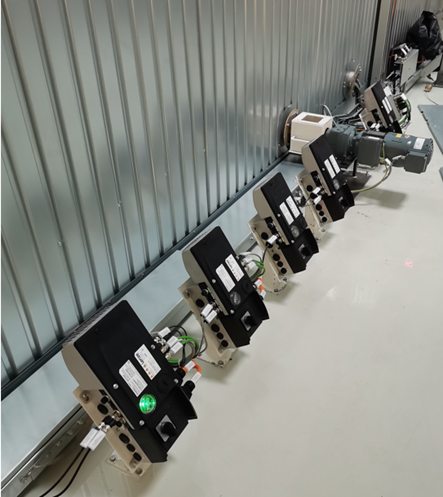
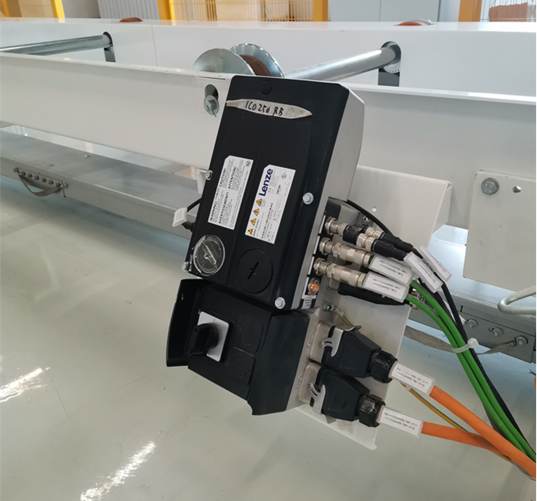
我们在现场每一个区域的电气控制柜中部署一台边缘计算机,向下通过Profinet网络接入变频器所在的总线网络中,每台边缘计算机可以接入多达100个变频器,向上通过工厂局域网,将采集到的变频器数据推送到部署在工厂中的私有云服务器中,该系统独立于现场的控制系统,不影响现存的网络架构,也不需要对现存的控制系统进行任何的修改。
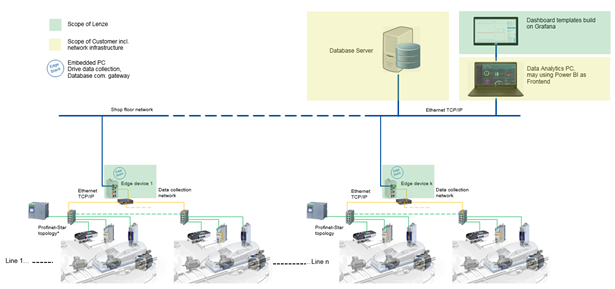
在边缘计算机中部署伦茨数字化团队开发的LSP(Lenze Service Portal) Gateway软件工具,采集现场变频器任意所需参数,并将这些参数进行清洗和封装成服务器熟悉的JSON格式数据,同时当网络中断时,可以将采集的数据进行缓存,待网络恢复后再将数据续传,保证数据的连续性。
在客户的中央控制室,我们部署了私有云服务器,通过MQTT协议将边缘计算机中的变频器数据,送入一个时间序列的数据库中,并通过基于Web浏览器的大屏展示工具,将这些数据展示在中控室的大屏幕中或者智能终端中,让客户方便的监控现场变频器的状态。所有的软件技术,均基于Docker容器技术开发部署,交付周期极短,从现场的硬件安装到调试完成,只用了一个星期,同时,客户产线正常生成,无需停机。
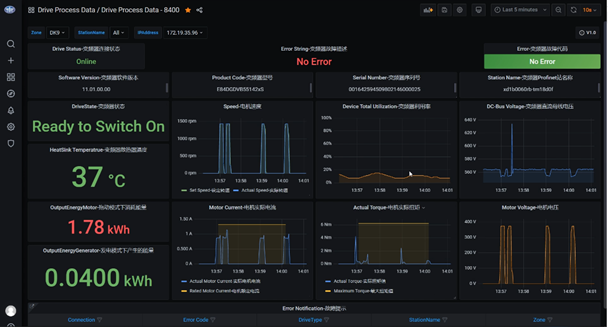
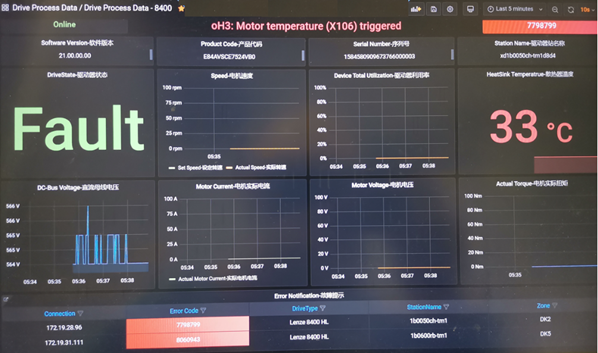
另外作为增值服务,伦茨数字化解决方案中,还提供了机器学习工具包,进行数据分析,我们提供了两种方法供客户选择:
基于模型的方法,将测量的实际值和预先计算好的模型结果进行比较,如果异常模式被检查到或超出某个偏差,则将其定义为异常,该种方法无需强大的算力,可直接将数据送入伦茨的C750控制器中进行运算。
基于数据的方法,机器学习算法根据测量的数据(例如电机速度、加速度、扭矩、位置和电流等)了解系统的正常状态,将实际值与此所学描述进行比较,以检测偏差。这种方式需要强大的算力,可以通过伦茨X500远程访问网关接入云端,进行云计算分析。
通过上述机器学习功能,我们能够对设备的异常和磨损状况进行分析和警示。
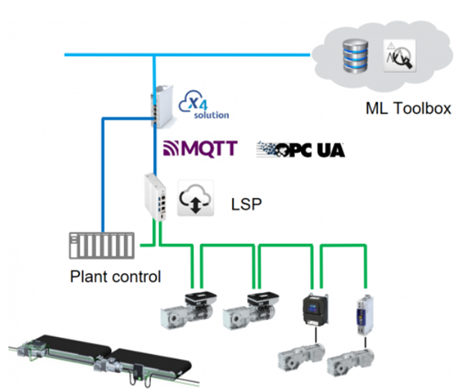
制造型企业面临着永久的挑战:如何确保系统高可用性、避免计划外的停机时间以及提前检测故障,同时最大限度地减少维护和检查工作?工业物联网和人工智能技术的发展提高了设备的可靠性和可用性,但是这些新技术的应用的前提是要获取关键设备的数据,然后对执行机构的数据采集是目前的难点,用户往往通过增加额外传感器至工业网关采集或者通过PLC进行数据采集,其实这些数据都已经在现场的驱动器里准备好了,伦茨开发的LSP gateway工具,很好的解决了现场大量变频器的数据采集难,可靠性差的痛点,并以得到实际项目的验证,另外在系统上层,我们准备了多种技术路线,确保数据高效率的存储和展示。
伦茨为客户提供的数字化解决方案,可以为用户提供以下帮助:
1. 获取设备的原始数据,通过部署在现场边缘计算机和伦茨LSP gateway软件包,用户无需对现存的系统进行任何的改动,消除由于控制系统的变化造成的停机风险。
2. 用户可以在工厂的控制室对现场所有运行的输送设备状态进行监控,快速查找故障问题,同时可以联系厂家远程协助排查故障。
3. 将现场每个工位变频器的型号,版本,参数,技术手册,所在位置等资产信息进行管理,方便后续的维护和检查升级,极大的提高了用户的工作效率。
4. 后续引入伦茨机器学习工具软件,可以对设备的健康状态进行分析,及时发现异常状况,提前预警,确保生产线的健康稳定运行。
跟帖
查看更多跟帖 已显示全部跟帖